In-mold decorating (IMD)
DuraTech creates custom solutions for in-mold decorating
In-mold decorating (IMD) provides original equipment manufacturers (OEMs) and molders an alternative method for decorating plastic parts. With IMD, graphics are printed on a film, using one or a hybrid of several printing processes, which is then inserted into a mold cavity. A compatible resin is then injection molded behind or over the decorated appliqué film, permanently embedding it into a molded part. The result is a highly durable, eye-catching part that provides a great user experience for human-machine-interface (HMI) applications. We create IMD solutions for customers in the automotive, home appliances, medical devices and consumer electronics industries.
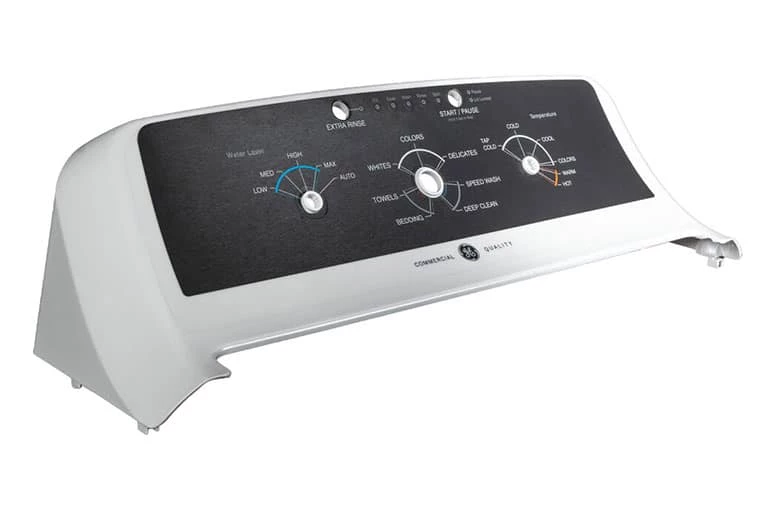
Start your next custom in-mold decorating project today!
Our custom IMD manufacturing capabilities
We can customize IMD parts to meet your exact specifications and create the unique user experience that will take your products to the next level. We offer a wide variety of finishes, colors and other graphics characteristics to align with your brand identity and application requirements. We use our industry-leading technology and durable graphics expertise to help you achieve your goals and create parts that will elevate your products above the competition.
Much of the success of any in-mold decorating project is the early development of the chosen suppliers and the concurrent development of all materials and processes. Remember to allow enough time to achieve your goals and contact us early in the process.
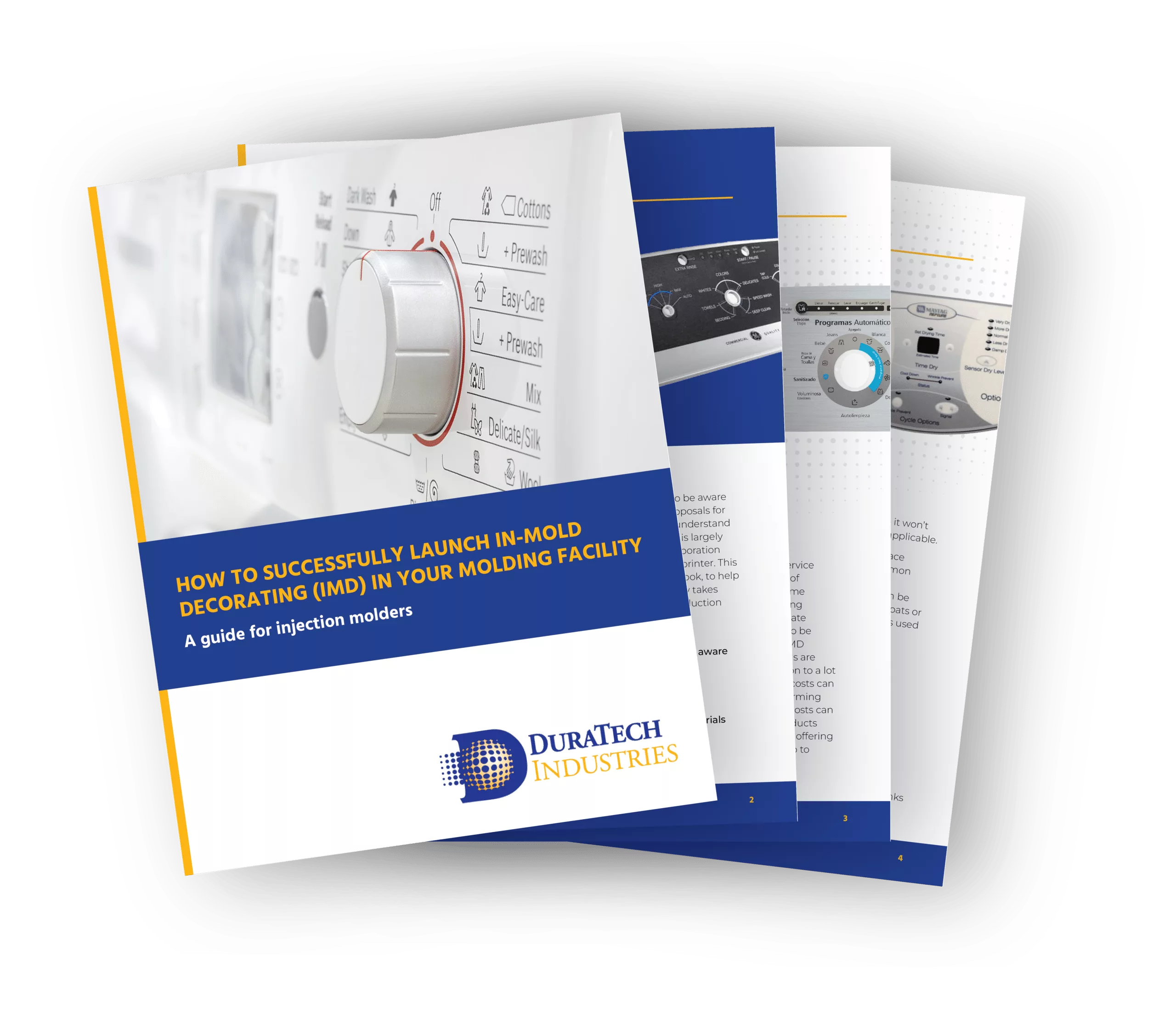
Ebook: How to Successfully Launch In-Mold Decorating (IMD) in Your Molding Facility
In-mold decorating (IMD) can be a valuable way to create aesthetically pleasing plastic parts. In the IMD process, graphics are printed on a film (or label) which is then inserted into a mold cavity. A compatible resin is then injection molded behind or over the decorated appliqué film, permanently embedding it into a molded part. The result is a single highly durable, eye-catching part. IMD products are used across industries for a wide variety of end-use applications.
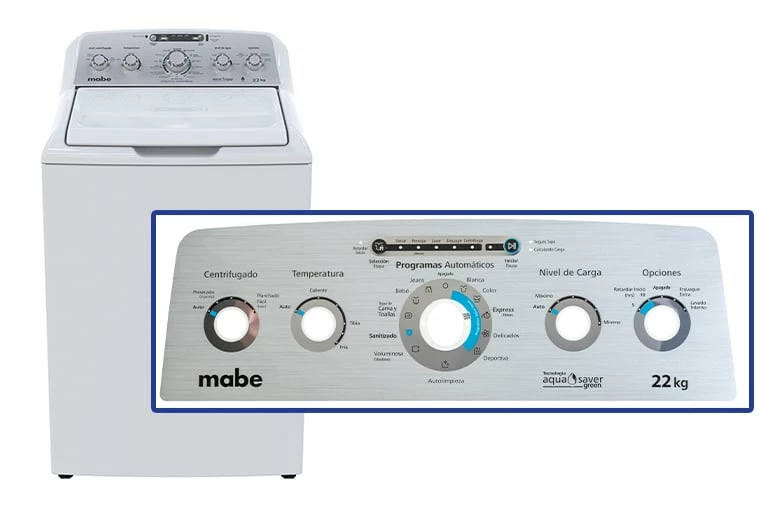
Featured Product
Custom IMD Graphic for Mabe
DuraTech created this custom IMD graphic overlay for a washing machine sold by the Mabe brand in South American markets. The part features a custom printed brushed pattern to enhance the product’s aesthetics and set the machine apart from competitors.
DuraTech solves ink cracking problem to keep in-mold label project on track
When TH Plastics was faced with a confusing and difficult in-mold labeling challenge, they needed a cost-effective solution, and quickly. “They had a very, very small processing window,” said BJ Tully, account manager at DuraTech. “We needed to find a solution that could keep the program on schedule.”
Common applications and benefits of IMD parts
IMD solutions are used in a wide variety of HMI applications, including consumer products like white goods and small appliances, tools, AC/heating components and recreational products. IMD solutions are ideal for high volume opportunities and any other HMI application that calls for enhanced durability and manufacturing efficiency.
The most significant benefits of custom IMD solutions revolve around greater design flexibility and manufacturing productivity.
Design Flexibility
- Product DifferentiationUnique graphics/looks
- Logos, model names, etc.
- Can use flat, curved or 3D labels or graphic overlays/decorative appliques
- Use of multiple colors
- Permanently embedded graphics
- Multiple models with one tool
- IMD can also be used in in-mold electronics (IME)
Manufacturing Productivity
- Eliminate secondary operations and labor
- Shoot and decorate part for life in one operation
- Eliminating adhesive (cost and process) can sometimes lead to lower unit pricing
- Lower systems cost in many applications (staging, inventory, etc.)
- Reduced inventory cost due to stocking one color of resin
Industries
IMD solutions are used across a wide range of industries because they provide a positive user experience and can be easily incorporated into full product designs. IMD parts can be used for a wide range of HMI applications, but are most commonly used in these industries:
IMD materials
The requirements for the film for an IMD application are much different than a standard adhesive-backed label. IMD solutions call for dimensionally stable film due to heat and pressures in the IMD process. Thinner films are typically used to avoid gate wash, while thicker films are used for deeper draws. IMD lends itself well to second surface printed vs first surface for greater durability. This is why UV, chemical and abrasion-resistant films play a greater role in IMD applications. 3-D IMD solutions require pre-formed inserts that may have even more specialized requirements, such as low-stress films, hard coating or depth to draw.
Commonly used IMD film types:
- Polycarbonate (PC)
- Acrylic
- Polyester
- Blends & Laminates
- PC-PET
- Acrylic Capped PC
Lower cost standard Film Alternatives:
- Polypropylene/Copolyester/PVC
Why choose DuraTech Industries
Manufacturers choose DuraTech for custom in-mold decorating solutions because we have the knowledge, experience and technical skill to create outstanding products with every production run. We live and breathe custom graphics solutions and use our passion to enhance our customers’ products and operations. Our materials science expertise and global reach provide exceptional value and help accelerate the product development process.
Ultimately, manufacturers choose DuraTech because they trust us to provide great products, a great experience and to deliver projects with unbeatable customer service.